Unlocking HVAC Efficiency: Comprehensive Maintenance Insights from Our Palm Desert Project
Unlocking HVAC Efficiency: Comprehensive Maintenance Insights from Our Palm Desert Project
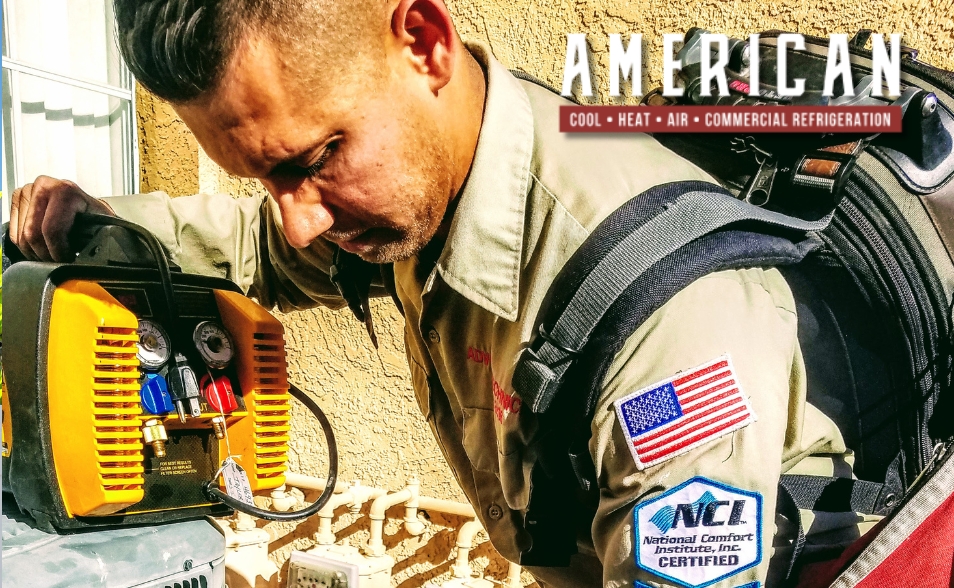
In the heart of Palm Desert, California, businesses rely heavily on their HVAC systems to maintain a comfortable environment year-round. However, many business owners overlook a critical aspect: regular maintenance of these systems. The consequences of neglecting HVAC maintenance can be costly, leading to inefficient performance, unexpected breakdowns, and even severe damage to the system or the building itself. But fear not; in this blog, we delve into the intricate process of a comprehensive commercial HVAC maintenance routine, showcasing our recent project in Palm Desert. With insights from our expert technicians, you’ll discover the essential steps to ensure your system’s longevity and efficiency. Stay tuned as we reveal the secrets to optimal HVAC performance and how our meticulous methods can save you from potential headaches and expenses.
The Importance of HVAC Maintenance
The rooftop of a commercial building in Palm Desert is where our team began a critical maintenance job on two package units: a five-ton Carrier unit and an older Lennox unit dating back to around 2008. While these units serve the same purpose, their condition and specifications vary, underscoring the importance of tailored maintenance.
The first step in our process is meticulous documentation. Each maintenance session is logged, capturing vital information such as the date, voltage, unit phase, location, refrigerant type, and serial and model numbers. This data is invaluable for tracking, ordering parts, and assessing the unit’s age. Using the same company consistently for maintenance ensures familiarity with your equipment, streamlining future repairs and replacements.
Our journey through the maintenance checklist begins with the blower section. Before any hands-on work, safety is paramount, so we ensure the disconnect switch is off, cutting power to the unit. Within the blower section, the belt’s condition and tension are checked. A half-inch play is ideal, and our inspection revealed a belt in good condition, free of cracks and dry rot—crucial for efficient operation.
We also examined the shivs, motor supports, and blower wheel bearings. Everything from wiring to fan blades was scrutinized to ensure optimal performance and safety. With no visible cracks or damage, the blower section was deemed in excellent condition. This thorough approach highlights the critical role of regular HVAC maintenance in preventing minor issues from escalating into costly repairs.
Filter and Economizer Inspection
Transitioning from the blower section, our focus shifted to the filter and economizer components of the units. Filters are the unsung heroes of HVAC systems, trapping dust, pollen, and other airborne particles to maintain indoor air quality. In this particular unit, we discovered four filters, slightly dirty, reminding us of the importance of routine replacement to combat allergens and ensure peak system performance.
Replacing filters is a straightforward task, yet it holds profound implications for system efficiency and air quality. Each new filter was carefully dated to maintain a precise maintenance schedule. A clean evaporator coil, as observed here, further underscored the unit’s relatively new status, though periodic brushing might be required to remove minor debris.
Adjacent to the filters, the economizer plays a pivotal role in energy efficiency. This component regulates fresh air intake based on outdoor temperatures, reducing reliance on compressors during cooler weather. We inspected and cleaned the economizer’s metal screen filters, crucial for preventing dirt accumulation. These screens, often overlooked, are instrumental in maintaining the unit’s longevity and efficiency. Over time, they can degrade, so regular checks and replacements every three to five years are recommended.
Our comprehensive inspection of these elements not only ensures clean air circulation but also enhances the system’s overall efficiency. By addressing these seemingly minor details, businesses can avoid unnecessary strain on their HVAC systems, resulting in lower energy bills and a more sustainable operation.
Condensate Management and Electrical Inspection
Next, we ventured to the rear side of the cooling unit to tackle a common but often neglected issue: condensate management. The condensate drain is a critical component that can lead to significant problems if obstructed. A blocked drain can cause water to overflow within the unit, potentially leading to interior water damage and costly repairs.
Our inspection revealed sludge accumulation in the drain trap, a common occurrence that underscores the necessity of regular maintenance. By flushing the trap with water, we removed the buildup, ensuring the condensate could flow freely. This simple yet vital procedure can prevent substantial damage and expenses, emphasizing the value of preventative maintenance.
Turning our attention to the electrical section of the unit, we examined the array of components that form the system’s nervous system. Ensuring the power was off for safety, we inspected the printed circuit boards, contactors, transformers, capacitors, thermostat logic board, and economizer module. Each component was checked for proper function, secure connections, and the absence of corrosion or damage.
This thorough electrical inspection is crucial, as even a minor fault can disrupt the system’s operation. By identifying potential issues early, we can address them proactively, preventing unexpected breakdowns and ensuring the HVAC system’s reliability and efficiency. Through diligent maintenance, businesses can safeguard their investment and maintain a comfortable environment for their operations.
Condenser and Compressor Examination
With the electrical and condensate components inspected, we moved to the condenser section, a crucial component responsible for heat exchange. The condenser coil often bears the brunt of environmental exposure, collecting dirt, dust, and pollen. This accumulation can significantly impair the unit’s efficiency, making regular cleaning essential.
At our Palm Desert site, the condenser coil displayed pollen buildup, despite the unit’s relatively new status. To address this, we applied a chemical cleaning solution designed to penetrate and dissolve stubborn grime. As the foam turned black, it was evident that the contaminants were being effectively extracted, restoring the coil’s functionality. This annual cleaning ensures the condenser can efficiently release heat, reducing energy consumption and preventing potential overheating issues.
Adjacent to the condenser coil, we inspected the compressor, the heart of the HVAC system. We checked for signs of refrigerant leaks, which typically manifest as oily, dusty spots on the piping. The absence of such signs assured us that the system was sealed and functioning correctly.
Further scrutiny involved examining the high and low-pressure lines, filter dryer, and crankcase heater. The safety devices appeared intact, and the compressor mounting bolts were secure, preventing vibrations that could lead to line breakage. With everything appearing in order, we proceeded to conduct a pressure check with our gauges to confirm the refrigerant levels and ensure the unit’s operational integrity.
This meticulous approach to condenser and compressor maintenance not only enhances system efficiency but also extends the equipment’s lifespan, providing peace of mind for business owners regarding their HVAC investments.
Compressor and Pressure Check
The compressor is the heart of the HVAC system. We inspected the compressor and verified that pressure switches were securely mounted. We also performed a refrigerant pressure check to confirm proper system charge. With a cool ambient temperature during the test, we observed the pressure levels, which indicated the system was correctly charged. Proper superheat and subcooling values were noted, confirming optimal performance.
In the event of abnormal pressure readings, such as both gauges showing zero, it could signify a significant refrigerant leak, necessitating immediate attention to prevent system damage. Conversely, minor discrepancies can often be rectified with a small refrigerant top-up and leak test, avoiding more extensive repairs down the line.
By regularly checking refrigerant levels and system pressures, we ensure the HVAC unit operates within its designed parameters, optimizing energy use and preventing the risk of compressor damage due to inadequate refrigerant levels. This practice underscores the importance of precise maintenance in prolonging system life and maintaining cost-effective operations.
Heating System Inspection
With the cooling components thoroughly assessed and maintained, we transitioned to the heating system inspection—essential for ensuring comfort during the colder months. The heating system, often overlooked until the winter chill sets in, requires careful attention to maintain safe and efficient operation.
We began by removing the panel to access the heat exchanger, a vital component where the burners’ flame heats the air circulated throughout the building. These tubes can develop cracks over time due to the constant heating and cooling cycles, which can lead to dangerous carbon monoxide leaks. Fortunately, our inspection revealed no such cracks or signs of rust, confirming the unit’s integrity.
Next, we examined the gas line and valve, ensuring all connections were secure and leak-free. The draft inducer motor, responsible for expelling combustion gases, was checked for proper operation and secure mounting. We also assessed the ignition system, including the sparker, which ensures reliable burner ignition. Each component was visually inspected and tested to ensure it functioned correctly.
With the visual checks complete, we activated the heating system to verify its performance. The draft inducer motor engaged, the burners ignited with a clean blue flame, and the blower motor circulated warm air throughout the system. A successful activation confirmed the system’s readiness for the heating season.
Finally, we measured the blower motor’s amperage, comparing it against the manufacturer’s specifications. The readings aligned well below the maximum allowed, indicating the motor was operating efficiently without undue strain.
This comprehensive heating system inspection not only ensures that the unit will perform efficiently throughout the colder months but also safeguards occupants from potential safety hazards, such as carbon monoxide exposure. Regular heating maintenance is a crucial aspect of overall HVAC care, providing peace of mind and comfort for building occupants.
Wrap-Up and Documentation
Having completed the comprehensive maintenance routine on both the cooling and heating components of the rooftop units in Palm Desert, we moved into the final phase of our process: documenting our findings and actions. This step is vital for maintaining a detailed history of each unit, aiding in future diagnostics and maintenance planning.
We meticulously logged every aspect of the maintenance visit. This included recording all the critical metrics, such as refrigerant pressures, amperage readings, and the condition of belts, filters, and coils. Notably, we documented the cleaning of condenser coils and economizer screens, as well as the inspection and testing of the heat exchanger and associated components.
This detailed documentation serves multiple purposes. It provides the building owner with a clear, comprehensive record of what was done during the maintenance visit, offering transparency and peace of mind. Additionally, it creates a valuable resource for future reference, helping technicians quickly understand the history and condition of the equipment during subsequent visits. This continuity is crucial for efficient troubleshooting and decision-making regarding repairs or replacements.
By maintaining such records, we ensure that every visit builds upon the last, creating a consistent and informed approach to HVAC care. This attention to detail not only enhances system reliability and performance but also extends the lifespan of the equipment, ultimately delivering significant cost savings and operational efficiency for businesses.
If you’re a business owner in Palm Desert or the surrounding areas, don’t wait until your HVAC system fails to take action
Regular maintenance is key to ensuring efficiency, safety, and longevity. Contact American Cool, Heat, Air & Commercial Refrigeration today. Our expert technicians are ready to tailor a maintenance plan that meets your specific needs, keeping your systems running smoothly year-round. Let us help you protect your investment and maintain a comfortable, energy-efficient environment for your business.
EXTENSIVE SERVICE COVERAGE FOR COMMERCIAL HVAC & REFRIGERATION SOLUTIONS
No Commercial HVAC or Refrigeration job is too small or too far for us. While our primary branches are located in Palm Desert and Rancho Cucamonga, California, we’re dedicated to reaching customers wherever they are in need.
Proudly serving cities across California, including Indio, La Quinta, Indian Wells, Bermuda Dunes, Thousand Palms, Cathedral City, Rancho Mirage, Santa Ana, Fontana, Moreno Valley, Glendale, Ontario, Garden Grove, Palm Desert, Irvine, Anaheim, Riverside, Palm Springs, and extending to Los Angeles and beyond. Your satisfaction is our priority, no matter the distance or scale of the project.
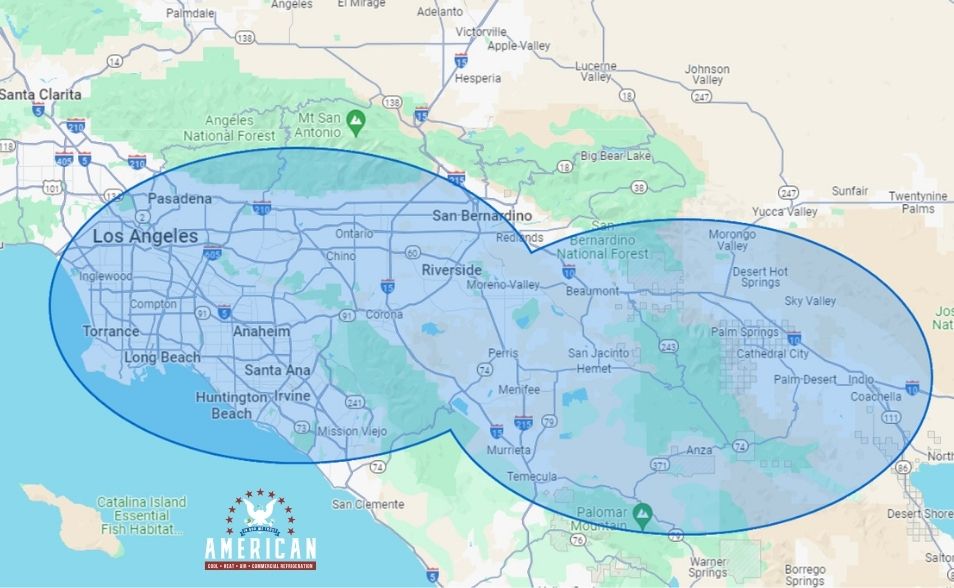
AMERICAN COOL HEAT AIR BRANCHES
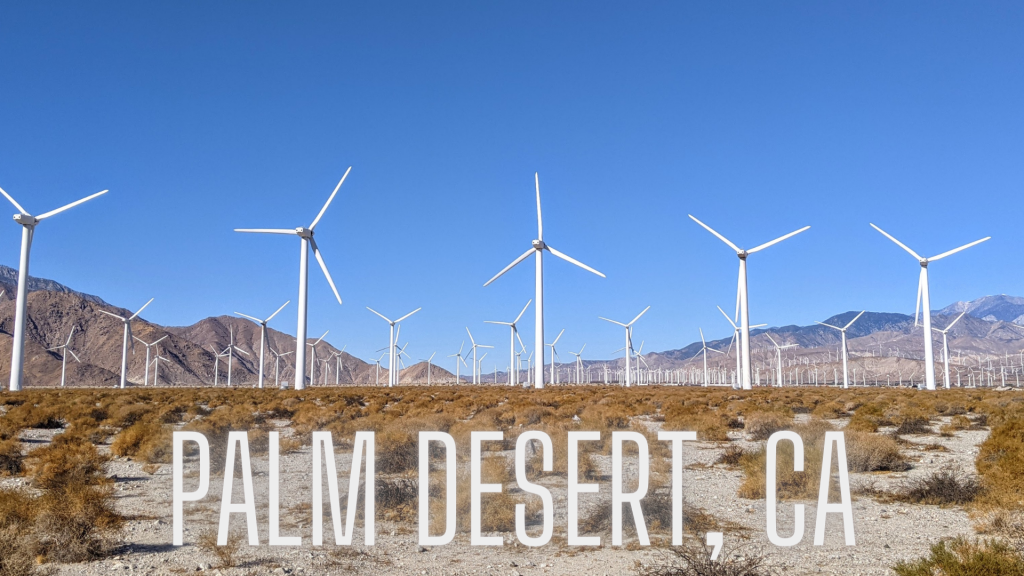
PALM DESERT, CA
77564 Country Club Dr. #142,
Palm Desert, CA, 92211
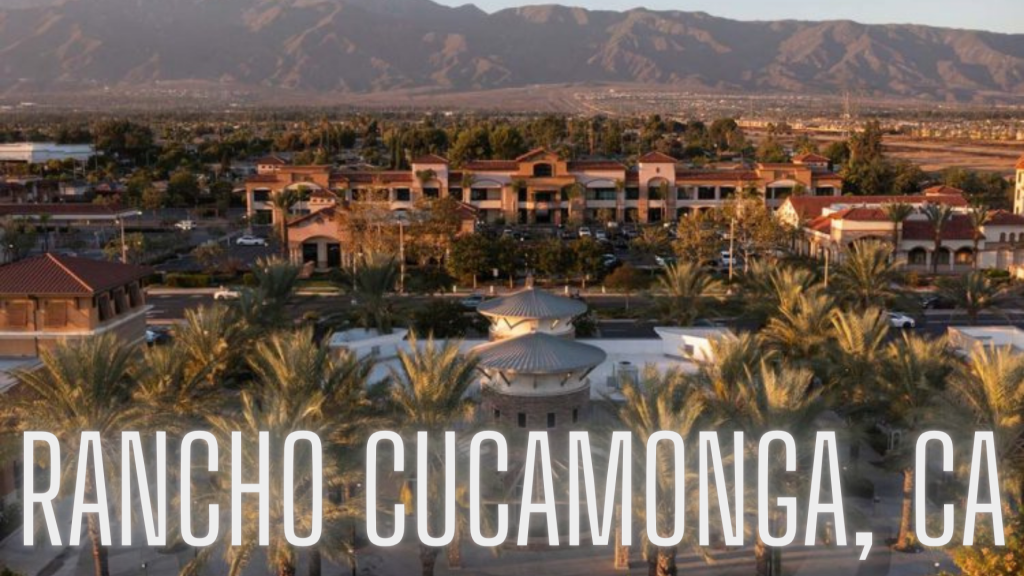
RANCHO CUCAMONGA, CA
10601 Civic center Dr 100H,
Rancho Cucamonga 91730